Why Choose Medical Parts Source ?
All long-term care and other healthcare facilities should have a proper Medical Equipment Maintenance Program in place. With budgetary issues, staff cutbacks and decreasing reimbursements, many facilities choose to avoid this expenditure. But this is a failure to recognize that it is a matter of good risk management, as well as being both a regulatory and accreditation compliance requirement.
Hospitals today typically have their own in-house biomedical engineers to service, maintain and inspect their equipment. Long-term care facilities do not have, or even need, an entire Biomedical Engineering Department, but they are still required to have their equipment properly maintained and tested.
The lack of ongoing preventive maintenance of medical equipment increases the risk of potential injury to patients or staff members caused by defective equipment. Most accrediting organizations such as The Joint Commission, AAAASF, HFAP, CHAP, CARF, and even the DOH, to name a few, require proper maintenance as indicated in their accreditation guidelines. While some refer simply to “properly maintaining” equipment, others such as TJC, are quite specific regarding the requirements.
As part of keeping your facility’s operating safe, periodic inspections should be performed. In addition to the periodic inspections, all equipment must be inspected prior to being placed into service and after any repairs. It is important to note that all equipment must be tested and documented, regardless of ownership (i.e. facility owned, leased, borrowed, etc.). The burden is on the facility, not the equipment provider.
The cost of having an ongoing program is far less than the costs and risks of not having one. While accidents can happen due to equipment failure; a safety program establishes a reasonable defense against negligence. Why risk the potential of lawsuits, higher insurance premiums, negative press, or regulatory deficiency citations? An Equipment Maintenance Program helps your facility create a safer environment. Proper management can improve the cost-effectiveness and utilization of your equipment by reducing downtime and minimizing equipment failures.
In dealing with medical equipment, it is crucial to be alert for signs of malfunction. Your resident’s health and safety may be at stake. Do your patient lifts have worn parts and are hazardous when lifting or moving a patient? Are your beds and wheelchairs free of exposed metal with sharp edges or loose parts which can cause accidental falls (i.e. loose wheelchair brakes)?
Price alone cannot be your main consideration. We suggest you consider the following, when choosing your parts provider.
- Do I have enough personnel to cover service and support functions?
- Who do my fellow peers use?
- How long has the company been in business?
- What are the knowledge levels of the customer support staff?
- How broad-based is their parts inventory? Do they specialize in only one type of equipment or can they provide parts a wide variety of equipment?
- Will they provide me with references?
- Can I reach ownership or management should the need arise?
Choose a company that has a track record of serving your industry. Longevity speaks volumes and over time your vendor will be there for you and stand behind their work. Medical Parts Source has been serving professional healthcare facilities since 1990. Choose your parts provider carefully and only after you have received satisfactory answers to the questions above.
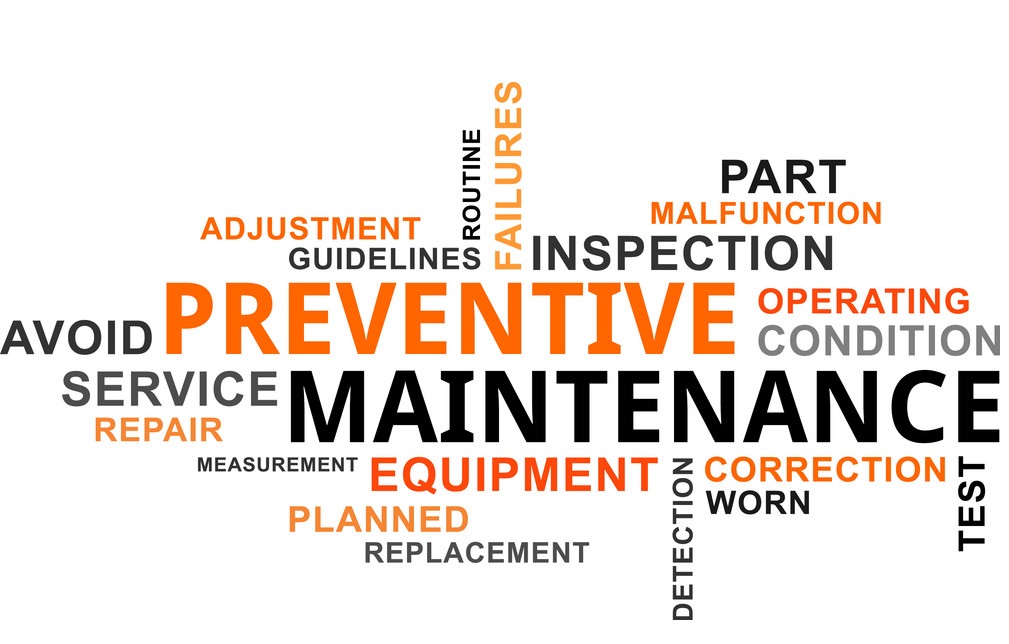